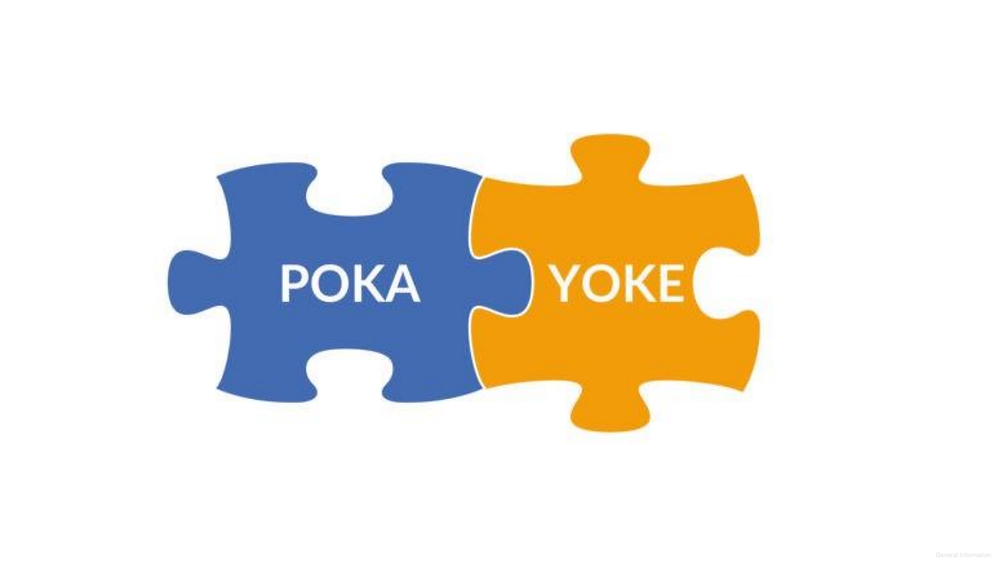
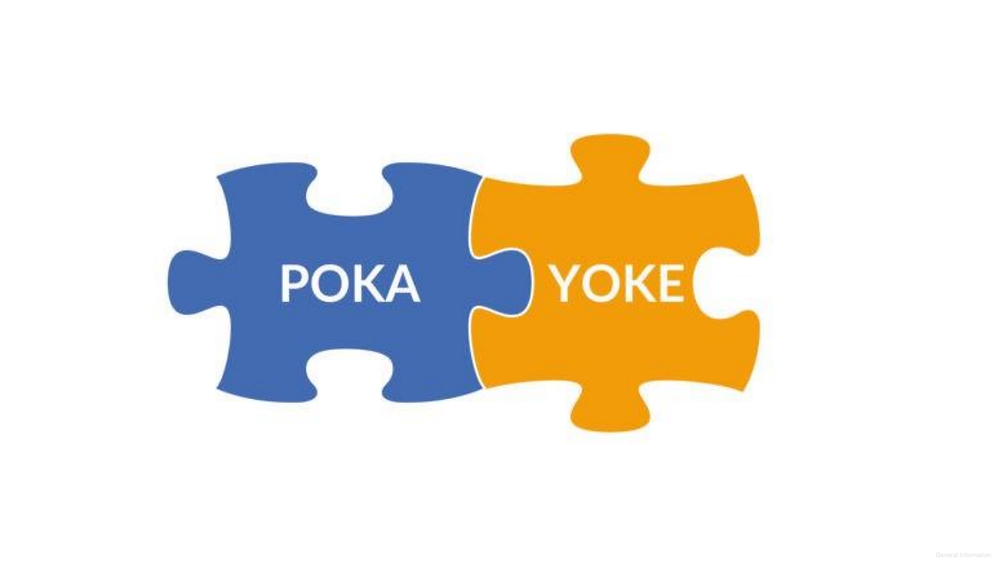
Poka Yoke in Modern Manufacturing: How Quinn Vietnam Manpower Helps Companies Eliminate Defects
- trienkhaiweb
- 17 May, 2024
- 0 Comments
In today’s competitive global manufacturing landscape, the term “Poka Yoke” is gaining traction. Derived from Japanese, it signifies “error-proofing” or “mistake-proofing.” Initially developed within Toyota’s renowned production system, Poka Yoke is a robust methodology that aims to enhance product quality and significantly mitigate risks throughout the manufacturing journey. At its core, Poka Yoke is about designing systems, processes, and even products in a way that proactively prevents errors from occurring in the first place.
The Origins of Poka Yoke
Poka Yoke traces its roots back to the 1960s when Shigeo Shingo, a pioneering industrial engineer, observed a simple yet consequential oversight on a factory floor. Workers had inadvertently omitted a spring from an on/off switch, leading to a domino effect of subsequent process failures. This incident crystallized Shingo’s understanding that even seemingly minor human errors could have far-reaching consequences.
Poka Yoke’s Pivotal Role in Production
-
Error Detection: No matter how meticulous human workers or sophisticated machines may be, errors are inevitable. Poka Yoke systems act as vigilant guardians, swiftly detecting anomalies and halting production before defective products emerge. This real-time feedback loop allows for immediate corrective action, minimizing waste and ensuring consistent quality.
-
Error Prevention: Poka Yoke takes a proactive stance against defects. By identifying potential failure points within a process, Poka Yoke solutions are implemented to eliminate or mitigate those risks. This may involve redesigning workflows, implementing sensors or guides, or establishing standardized procedures. The result is a manufacturing environment where errors are less likely to occur in the first place.
-
Error Correction: In cases where minor errors do occur, Poka Yoke mechanisms can often rectify the issue automatically or with minimal human intervention. This not only saves valuable time but also reduces the burden on employees, allowing them to focus on higher-value tasks.
Quinn Vietnam Manpower: Your Partner in Poka Yoke Implementation
Quinn Vietnam Manpower, a leading specialist in labor export, recognizes the transformative potential of Poka Yoke in modern manufacturing. We understand that a skilled and well-trained workforce is essential for successful Poka Yoke implementation. Our comprehensive services include:
- Recruitment and Selection: We identify and recruit top-tier talent with the expertise and adaptability to thrive in Poka Yoke-driven environments.
- Training and Development: Our customized training programs equip your workforce with the knowledge and skills necessary to understand, implement, and continuously improve Poka Yoke strategies.
- Process Optimization: We collaborate with your team to analyze existing processes, identify vulnerabilities, and design effective Poka Yoke solutions that align with your specific production goals.
The Six Principles of Poka Yoke
Poka Yoke operates on six fundamental principles:
- Elimination: Redesigning products or processes to remove potential error sources entirely.
- Prevention: Implementing measures that make errors impossible or extremely unlikely to occur.
- Replacement: Substituting a problematic process with a more reliable or error-resistant alternative.
- Facilitation: Making it easier for workers to perform tasks correctly through intuitive design and clear instructions.
- Detection: Employing sensors, checks, or inspections to identify errors as they occur.
- Mitigation: Minimizing the impact of errors when they do happen, preventing them from propagating further down the production line.
When to Apply Poka Yoke
Poka Yoke can be applied to virtually any industry or process where errors have a significant impact on quality, cost, or safety. Here are some scenarios where Poka Yoke implementation is particularly valuable:
- High-Value Products: When the cost of a defective product is substantial, Poka Yoke can safeguard your investment.
- Safety-Critical Processes: In industries like automotive or aerospace, where errors can have dire consequences, Poka Yoke is paramount.
- Complex Processes: Processes with multiple steps or intricate operations are prone to errors, making Poka Yoke an invaluable tool.
- Repetitive Tasks: Poka Yoke helps maintain consistent quality even in monotonous tasks where human attention may waver.
A Step-by-Step Guide to Poka Yoke Implementation
- Identify the Problem: Pinpoint the specific error or defect you want to address.
- Root Cause Analysis: Investigate the underlying reasons behind the error.
- Choose a Poka Yoke Method: Select the most appropriate Poka Yoke principle or technique for your situation.
- Design and Test: Develop your Poka Yoke solution and thoroughly test its effectiveness.
- Train Your Workforce: Ensure your employees are well-versed in the new process and its rationale.
- Monitor and Improve: Continuously track the results and refine your Poka Yoke system as needed.
The Quinn Vietnam Manpower Advantage
Partnering with Quinn Vietnam Manpower for your Poka Yoke journey offers a distinct advantage. We combine our deep understanding of workforce dynamics with our expertise in manufacturing processes to deliver tailored solutions that drive tangible results.
Conclusion
Poka Yoke isn’t just a buzzword; it’s a proven methodology that empowers companies to achieve manufacturing excellence. By embracing Poka Yoke and leveraging the expertise of Quinn Vietnam Manpower, you can unlock a future of higher quality, reduced costs, and enhanced competitiveness.
Remember: In the pursuit of error-free manufacturing, the key is not to eliminate workers but to empower them with the tools and knowledge they need to succeed. Poka Yoke, facilitated by Quinn Vietnam Manpower, is that empowering tool.
Related articles
Making Critical Decisions for Manpower Management: A Guide for Quinn Vietnam Manpower’s Partners
In the ever-evolving landscape of manpower management, making informed decisions is crucial for success. Whether you’re a seasoned HR professional or a business leader navigating the complexities of workforce planning, the choices you make today will shape the future of your organization. This guide, tailored for Quinn Vietnam Manpower’s valued partners, provides a comprehensive framework…
Mastering Communication for Effective Manpower Management: The 5 Chairs Model
In the competitive landscape of 2025, effective communication is more critical than ever for successful manpower management. At Quinn Vietnam Manpower, we recognize that clear, empathetic, and strategic communication is the cornerstone of building strong teams, fostering productivity, and achieving organizational goals. This article explores a powerful communication model, the “5 Chairs” by Louise Evans,…
Mastering Communication Styles for Effective Leadership: A Guide for Quinn Vietnam Manpower Clients
In today’s dynamic business landscape, effective communication is paramount to success. This is especially true for leaders and managers navigating the complexities of the modern workplace. At Quinn Vietnam Manpower, we understand the crucial role communication plays in building strong teams and achieving organizational goals. That’s why we’ve prepared this comprehensive guide to help you…
Mastering Delegation: 5 Principles for Success with Quinn Vietnam Manpower
In today’s dynamic business environment, effective delegation is a critical skill for any manager. As we move into 2025, the ability to assign tasks efficiently and empower your team is more crucial than ever. This is particularly true when working with a diverse workforce, such as the skilled professionals provided by Quinn Vietnam Manpower. This…
A Guide for Quinn Vietnam Manpower Clients To Mastering Delegation
In today’s dynamic business landscape, effective delegation is more critical than ever. For our valued clients at Quinn Vietnam Manpower, understanding and implementing strong delegation strategies can significantly impact your organizational success in 2025. While many managers recognize the importance of delegation, knowing how to delegate effectively is a different story. This article provides a…
Mastering Delegation: A Guide for Quinn Vietnam Manpower
Effective delegation is a cornerstone of successful leadership and increased productivity in any organization, and Quinn Vietnam Manpower understands this principle deeply. As we step into 2025, the ability to delegate effectively becomes even more critical in navigating the evolving landscape of the manpower industry. This involves understanding company objectives and strategically breaking them down…